Utilizzo di nanoparticelle nelle fasi conciarie e tecniche di dispersione di laboratorio
L’utilizzo di nanoparticelle per la funzionalizzazione dei materiali, con particolare riferimento ai polimeri, è diffuso in numerosi settori industriali. Utilizzando i classici processi conciari, le nanoparticelle potrebbero trovare applicazione sia nelle fasi ad umido che in quelle di rifinizione per ottenere proprietà specifiche che non prevedono l’utilizzo di chemicals. Il problema principale nell’uso delle nanocariche è quello di ottenere una corretta disaggregazione ed omogenizzazione delle stesse in un mezzo disperdente che, nel nostro caso, può essere rappresentato dagli ingrassi e resine di riconcia nelle lavorazioni in botte e dei formulati di rifinizione da applicare successivamente a spruzzo o a rullo. Molte nanocariche, per caratteristiche intrinseche (es. grafene, o nanotubi) si presentano sotto forma di aggregati con legami secondari che devono subire un processo di separazione per poter essere utilizzati. Esistono differenti tecniche di trattamento delle nanoparticelle e la loro scelta può dipendere dalle caratteristiche del materiale disperdente quale ad esempio la viscosità; quello più comunemente utilizzato in laboratorio è la sonicazione ad alta intensità e bassa frequenza.
Il sonicatore è un dispositivo che produce onde di ultrasuoni che si propagano nella soluzione da processare. Il principio di funzionamento prevede l’oscillazione delle molecole del mezzo disperdente nella loro posizione media per effetto degli ultrasuoni che determinano una variazione delle distanze relative tra le particelle costituenti. L’energia viene trasmessa, quindi, alle molecole che urtano con le nanocariche (es. nanoplatelets di grafene) contribuendo all’attivazione di fattori termodinamici che promuovono la loro corretta separazione/esfoliazione e dispersione. La propagazione degli ultrasuoni nella sostanza provoca azioni combinate di forze di taglio, differenziali di pressione e temperatura e turbolenze (forze cavitazionali) che accelerano le particelle con conseguente collisione e frantumazioni delle stesse. Quando la sonicazione viene eseguita con una sonda, il processo è sempre associato ad una agitazione meccanica finalizzata a garantire che l’azione localizzata sia applicata sull’intero volume di materiale, prevenendo altresì la precipitazione e la riaggregazione delle eventuali cariche disperse, nonché eventuali degradazioni della matrice. Aumentando il tempo di sonicazione si va verso agglomerati sempre più piccoli fino ad arrivare idealmente ad una fase monodispersa.
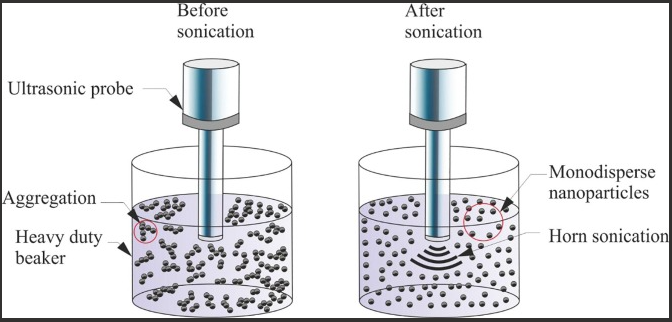
I parametri che influenzano la sonicazione sono: la potenza impostata, la frequenza di applicazione, ed il numero di cicli di sonicazione (tempo); in particolare, fissate le prime due variabili, la riduzione delle dimensioni delle particelle aumenta all’aumentare dei tempi di applicazione. Su scala laboratorio, esistono due tipi di sonicatori principali: il bagno ad ultrasuoni, nel quale la soluzione viene immersa in un apposito contenitore e la sonda sonicatrice che, invece, viene immersa direttamente nella soluzione. La differenza tra i due dispositivi è in termini di potenza massima: mentre la sonda sonicatrice consente una potenza compresa tra 100 W e 1.500 W, il bagno lavora a potenze inferiori, ovvero di circa 100 W. Se consideriamo la potenza, come precedentemente accennato, è necessario tenere in considerazione due importanti aspetti: l’utilizzo di elevate potenze e le applicazioni prolungate che, in entrambi i casi, possono determinare il danneggiamento delle particelle e la possibile degradazione mezzo disperdente per effetto del riscaldamento localizzato. Questi effetti possono essere limitati lavorando non con un’applicazione in continuo, ma in modalità pulsante nella quale gli intervalli di sonicazione in potenza sono intervallati da pause predeterminate. Questo tipo di procedura risulta generalmente utilizzabile per soluzioni a bassa viscosità, per cui il mezzo disperdente è opportuno che sia si trovino in miscela con solventi quali acqua, acetone o etanolo.
Per verificare l’applicabilità dei processi, la Stazione Sperimentale ha effettuato diverse sperimentazioni utilizzando prodotti di riconcia e di rifinizione caricate nanoparticelle carboniose (MWCNT e GNP). In particolare, sono state effettuate dispersioni con concentrazioni superiori rispetto a quanto solitamente eseguibile in solvente poiché la viscosità dei chemicals (es. ingrassi) contribuisce alla mancata riaggregazione delle nanocariche. Inoltre, sono state eseguite dispersioni utilizzando sia sonicatori a bagno che a sonda, con potenze di bassa intensità per evitare degradazioni del mezzo (es. resine liquide di riconcia). Le prove eseguite hanno fornito risultati molto promettenti sia per i prodotti da botte (resine e ingrassi) che per quelli di rifinizione. In quest’ultimo caso, una dispersione ed esfoliazione efficace non solo consente l’ingegnerizzazione delle proprietà superficiali, ma anche l’assenza di aggregati che rendono il prodotto cuoio merceologicamente idoneo per l’assenza di aggregati visibili ed assimilabili a difetti puntuali indesiderati.
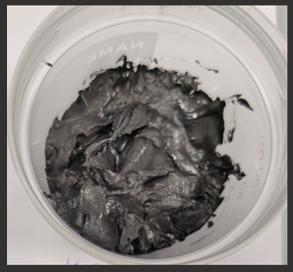
Quanto decritto rappresenta un punto di partenza per nuovi studi sull’uso di nanoparticelle nelle lavorazioni conciarie. Lo scale up dei processi consentirà l’applicazione delle nanoparticelle con differente funzionalità per la produzione di nuove generazioni di materiali innovativi.
A cura di
Ing. Rosario Mascolo – Coordinatore Tecnico-Scientfico Dipartimento Sviluppo Prodotto
Pubblicato il: 2 Ago 2023 alle 09:41