La produzione di rigenerato “Salpa” Vs costruzione di TNT da fibre di cuoio
Il CEN (Comitato Europeo di Normazione) ha stabilito che la terminologia corretta per indicare il cuoio rigenerato sia “rigenerato di fibre di cuoio”. E lo ha definito come: “materiale costituito da pelli conciate disintegrate meccanicamente e/o chimicamente in particelle fibrose, piccoli pezzi o polveri e, successivamente, con o senza la combinazione di legante chimico, trasformato in fogli”
Il processo per creare un rigenerato chiamato anche “SALPA” e costituito da diversi passaggi:
Macinazione
I ritagli di cuoio finito vengono sminuzzati a secco in un mulino a lame e stoccati. Da questo vengono avviati ad una seconda fase di macinazione a secco per avere uno sfibramento più spinto. Tale polvere viene quindi dispersa in acqua per avere un impasto con un tenore in sostanza secca di circa il 4%. Gli scarti di rasatura, invece, vengono macinati ad umido in un mulino a martelli.
Entro speciali vasche le polveri ottenute vengono miscelati in opportuni rapporti con opportuni additivi chimici per stabilizzare ulteriormente le fibre. Questo processo può essere effettuato per aggiunta di tannini vegetali o sintetici e ingrassi.
L’impasto ottenuto nelle vasche viene sottoposto ad un ulteriore processo di sfibramento, denominato raffinazione, mediante raffinatori conici che hanno il compito di separare tra loro e sminuzzare le singole fibre, in modo da avere la maggiore superficie di contatto possibile tra queste e i leganti che vengono successivamente introdotti.
Formazione del foglio continuo
L’impasto raffinato è opportunamente addizionato con leganti, quali lattice e resine sintetiche, e viene provocata la aggregazione tra le fibre e additivi chimici attraverso l’aggiunta di un agente coagulante (solfato di alluminio); viene quindi inviato alle macchine continue per essere trasformato in un foglio di cuoio rigenerato. Il processo successivo è infatti similare alla tecnologia utilizzata per la produzione della carta. L’impasto viene quindi uniformemente distribuito su una tela filtrante che ha il compito di formare il foglio di prodotto e fargli perdere gradualmente l’acqua. La parte terminale del processo presenta due presse a rulli che tolgono ulteriore acqua dal foglio, dove la velocità di avanzamento della tavola piana determina lo spessore del prodotto.
Pressatura in continuo del foglio
A questo punto il foglio di prodotto ha assunto una consistenza tale da non necessitare più del supporto della tela di formazione ma comunque necessita di perdere ulteriore acqua. Passa perciò attraverso due presse a rulli che lavorano a pressioni più elevate rispetto alle precedenti presse poste in coda alla tavola piana.
Forno di essiccazione del foglio
Dopo aver estratto buona parte dell’acqua attraverso l’azione delle presse, il foglio continuo attraversa un forno a temperature variabili da 100 a 130 °C. Il forno lavora con aria riscaldata indirettamente da vapore, laddove il prodotto perde gran parte dell’umidità residua.
Avvolgimento bobine di cuoio rigenerato
All’uscita del secondo forno il foglio di cuoio rigenerato è avvolto in bobine industriali, costituenti il prodotto grezzo. In questa fase il foglio continuo viene rifilato sui bordi per eliminare la parte di prodotto non adeguata ai successivi utilizzi.
Calandratura bobine di cuoio rigenerato
Il prodotto in bobine viene generalmente sottoposto ad una azione di schiacciamento facendolo passare attraverso due rulli (calandratura). Questa operazione ha il fine di dare uniformità trasversale allo spessore del prodotto, oppure di imprimere sulla sua superficie particolari disegni o effetti superficiali.
Smerigliatura bobine di cuoio rigenerato
Alcuni articoli vengono sottoposti ad abrasione superficiale per conferire un particolare effetto al prodotto. Questa operazione è condotta con macchina smerigliatrice.
Taglio bobine di cuoio rigenerato
L’operazione è eseguita con una apposita taglierina e il prodotto in fogli è pallettizzato ed immagazzinato.
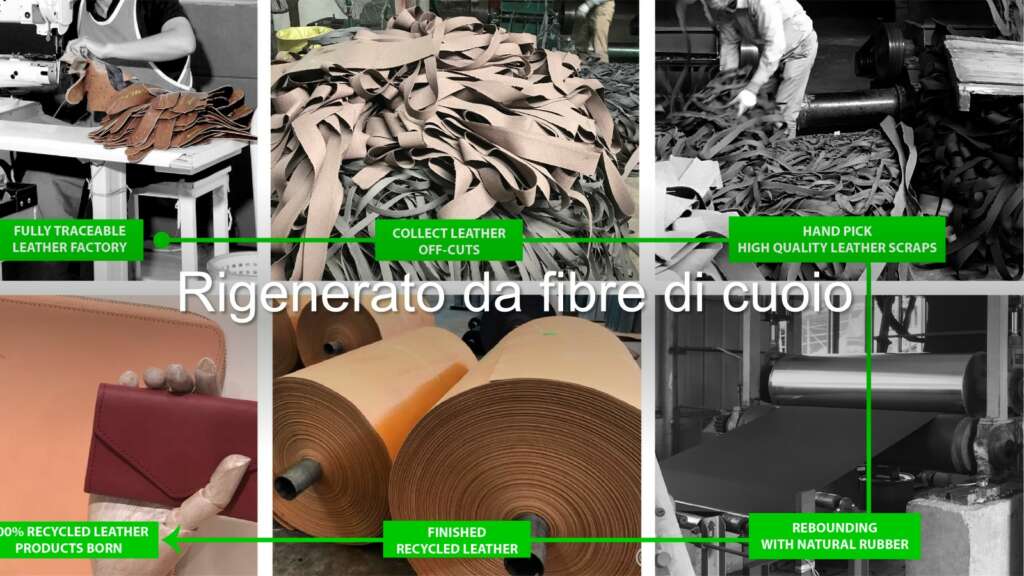
Il processo per creare un Tessuto-Non Tessuto (TNT) attraverso la lavorazione meccanica di fibre di pelle scarto segue invece procedimenti differenti:
Raccolta dei rifili di pelle di scarto:
In questo caso si tratta di prodotto che può essere costituito da rifili delle lavorazioni conciarie del reparto finito (pelle rifinite) o degli utilizzatori dello stesso (calzaturifici, salottifici, pelletterie ecc.)
Macinazione dei rifili
Trattamento meccanico atto a ridurre di dimensione opportuna alla successiva cardatura i rifili collettati.
Cardatura Airlay
La tecnologia airlay impiegata nello specifico progetto “Now Let’s Go” è una delle principali tecniche di produzione di tessuti non tessuti, caratterizzata dall’uso dell’aria come mezzo di distribuzione delle fibre. Questo metodo inizia con la preparazione delle fibre, che possono essere naturali, come appunto il cuoio, il cotone e lana, o sintetiche, come poliestere e polipropilene. Le fibre vengono aperte, pulite e separate per creare un flusso uniforme, pronte per essere alimentate in una camera di distribuzione. All’interno della camera, un flusso d’aria ad alta velocità disperde le fibre su una superficie di raccolta. L’aria turbolenta permette una distribuzione omogenea delle fibre, formando un velo uniforme. La densità e lo spessore del velo possono essere controllati regolando la velocità del flusso d’aria e del nastro trasportatore. Il velo di fibre viene poi consolidato attraverso vari metodi. Uno dei più comuni è l’uso di aghi (needlepunching), che perforano il velo intrecciando le fibre e creando legami meccanici che conferiscono maggiore resistenza e stabilità al tessuto. Un altro metodo è la legatura termica (thermobonding), dove il velo viene riscaldato in un forno, causando la fusione parziale delle fibre sintetiche che creano legami termici. Esiste anche la legatura chimica (chemical bonding), che utilizza leganti chimici spruzzati sul velo e poi asciugati per creare legami chimici tra le fibre. Dato che la pelle ha un comportamento proprio per cui non è possibile effettuare la lavorazione con una macchina Airlay tradizionale, nel particolare caso viene adeguato l’
l’Arilay con accorgimenti meccanici inerenti alla fluidodinamica interna per garantire una omogenea distribuzione delle fibre.
La tecnologia airlay offre vari vantaggi, tra cui la capacità di lavorare con una vasta gamma di fibre naturali e sintetiche, la produzione di un velo di fibre uniformemente distribuito che migliora le proprietà meccaniche del tessuto, l’efficienza del processo con capacità di produzione elevate e costi ridotti, e la possibilità di personalizzare la densità e lo spessore del tessuto in base alle esigenze applicative.
Taglio e rifilatura
Infine, il TNT viene tagliato e formato secondo le dimensioni e le forme richieste per l’applicazione finale.
Rifinizione superficiale del TNT
Il pannello realizzato può essere successivamente rifinito o rivestito superficialmente, mediante diverse tecniche, allo scopo di migliorarne le caratteristiche di aspetto, mano e conformità alle eventuali specifiche di solidità in relazione all’uso a cui è destinata. Ad esempio, nel progetto “Now Let’s Go” si è presa in esame la rifinizione via laminazione a secco, un processo che permette una notevole riduzione dei bisogni energetici ed un azzeramento della produzione di reflui liquidi.
Questa modalità di rifinizione, inoltre, permette una scelta di effetti finali molto ampia, dai fondi pieni agli effetti di riflettanza metallica, effetti olografici e tattili.
A cura di Marco Nogarole
Responsabile Trasferimento tecnologico della SSIP
Pubblicato il: 24 giugno 2024 alle 14